Rubber testing
ERT has a well-equipped laboratory with all possible advanced equipment and know-how for testing rubber products and compounds. Our employees are academically trained and/or have many years of practical knowledge and experience in the rubber industry.
Our customers come from the whole rubber chain: from raw material suppliers, manufacturers and end-users of rubber products to trading and recycling companies.
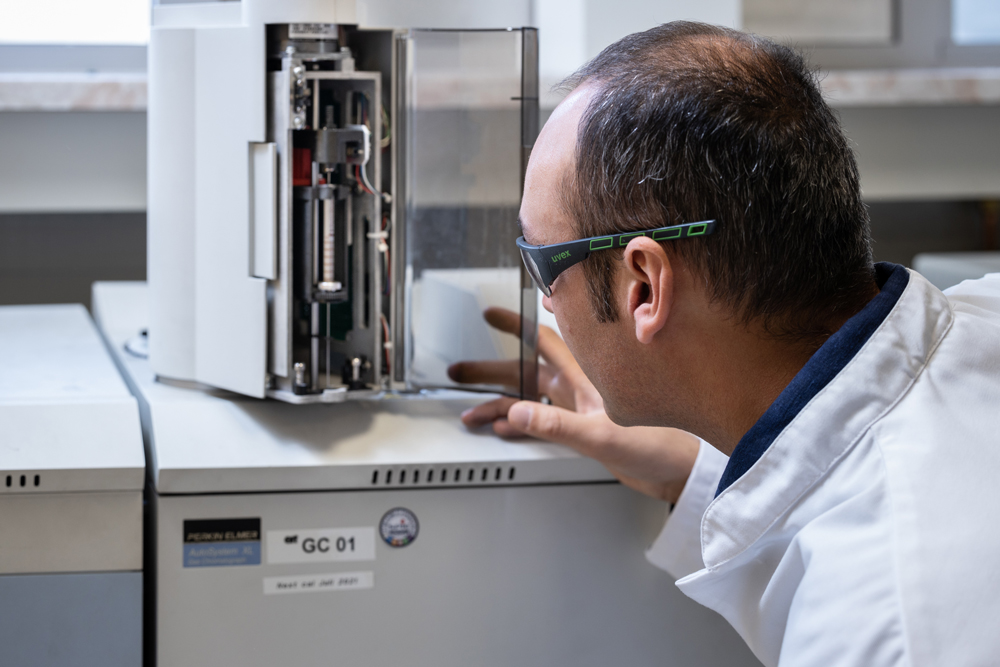
Tests on unvulcanised rubber

Chemical analysis
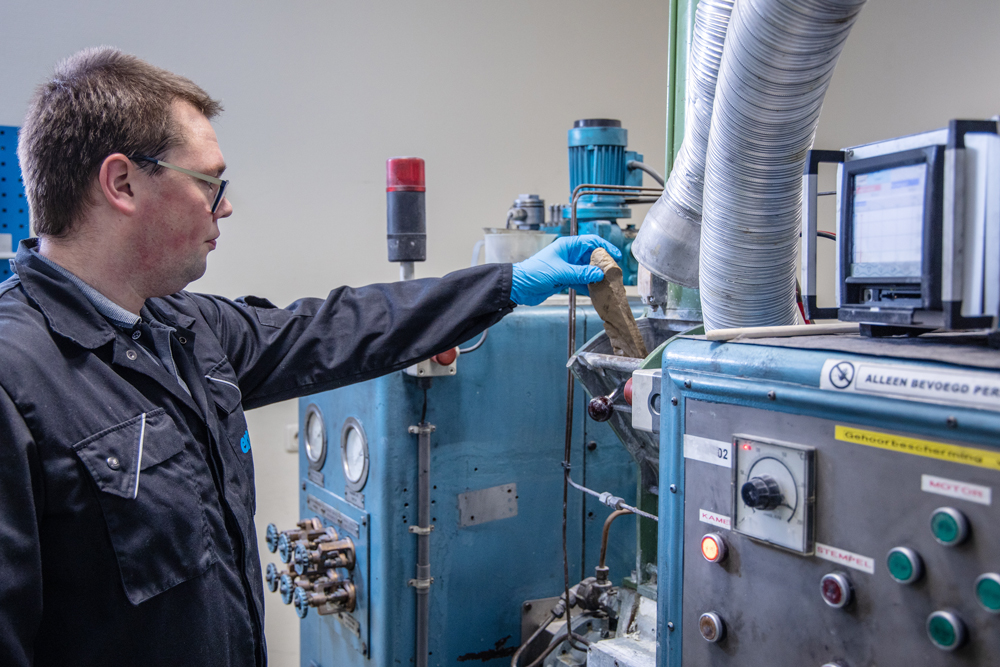
Dynamic properties

Physical and mechanical properties

Environmental and/or ageing impact

Other tests
We will be happy to help you
Location
Elastomer Research Testing BV
Teugseweg 27
7418 AM Deventer the Netherlands
Postal address
Elastomer Research Testing BV
PO Box 2149
7420 AC Deventer the Netherlands
Contact
E info@ertbv.com
T +31 570 62 46 16
F +31 570 62 57 02
